THE IMPORTANCE OF MANAGING SEQUENTIAL TASKS IN A DEALERSHIP
In many dealerships, the sequence of tasks related to receiving and shelving inventory is dictated by the attitude that “we’ve always done it that way.” Ken Ackerman, logistics and warehousing expert shares his ideas on how changing the sequence in which work is performed can significantly impact operations.
Ackerman suggests a “diagnostic examination of operations” that consists of by asking the following five questions regarding each of your current tasks that are part of an established sequence:
- Who does this job?
- Where is this job done?
- How is the task performed?
- When is it performed?
- Why is it done that way?
For example, what is the best sequence for moving merchandise from dock to stock? Is the staff member receiving the inventory provided with the information about where to store the inbound item? For more examples to consider that may be similar to the processes at your dealership or warehouse, see the full article by Ackerman.
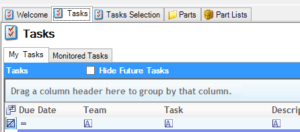
In the ASPEN dealership management system, equipment and material handling supply dealers can use the system’s task setting and monitoring functions to create their own workflows for their unique sequential tasks.
A Workflow is an automated task and transaction-creating process. As a user(s) complete their assigned task(s), they may continue the workflow by creating a follow-up task for themselves, another user or team. This is a great way to stay on top of processes in your dealership.
Upon logging into the ASPEN business system, users can view their assigned tasks as well as the areas they may be monitoring.
ASPEN’s tasks replace e-mails, notepads and sticky notes so nothing falls through the cracks, and help dealers to create more consistent processes for repetitive transactions.